A Single Point Mooring Buoy consists of a buoy that is permanently moored to the seabed by means of multiple mooring lines/anchors/chains allowing cargo transfer of liquid petroleum products. The buoy contains a bearing system that allows a part of it to rotate around the moored geostatic part. When a Ship is moored to this rotating part of the buoy with a mooring connection, the vessel is able to freely weather-vane around the geostatic part of the buoy.
Responsibility
Master has the overall responsibility for the mooring operations of the vessel at the SBM.
The officer-in-charge of forward and aft stations is responsible to the Master for supervising mooring operations at their station. They should ensure that the operation is conducted safely.
The Chief Officer shall ensure that all mooring wires, ropes and associated mooring equipment are well maintained and protected from weather and exposure damage.
SPM Components
The SPM system consists of four main components:
- Buoy body
- Mooring and anchoring elements
- Product transfer system
- Ancillary Components
Buoy Body
The buoy body is held in place by means of static legs attached to the seabed underneath the surface. The body has a rotating part above water level connected to the offloading/loading tanker. These two sections are linked by a roller bearing, referred to as the Main Bearing. The moored tanker can freely weather-vane around the buoy and find a stable position due to this arrangement.
The type of bearing used and the split between the rotating and geostatic parts determines the concept of the buoy. The size of the buoy is a function of the counter buoyancy needed to hold the anchor chains in position, and the chains are a function of the environmental conditions and the vessel size.
SPM Mooring to Seabed
Moorings fix the buoy to the seabed. The type of anchoring system is greatly dependent on local soil conditions and may consist of ships-, rig-, piles- or gravity anchors.
The two main types of mooring configurations for SPMs are Catenary Anchor Leg Mooring (CALM) and Single Anchor Leg Mooring (SALM). CALM holds the buoy in place by anchor chain that extends in catenaries to anchor points some distance from the buoy.
The SALM system is similar, except that the SALM is anchored by a single anchor leg. The primary benefit of a CALM Buoy over a SALM Buoy is ease of maintenance. The vast majority of Marine Terminals installed since the mid-1990s have been CALM Buoys.
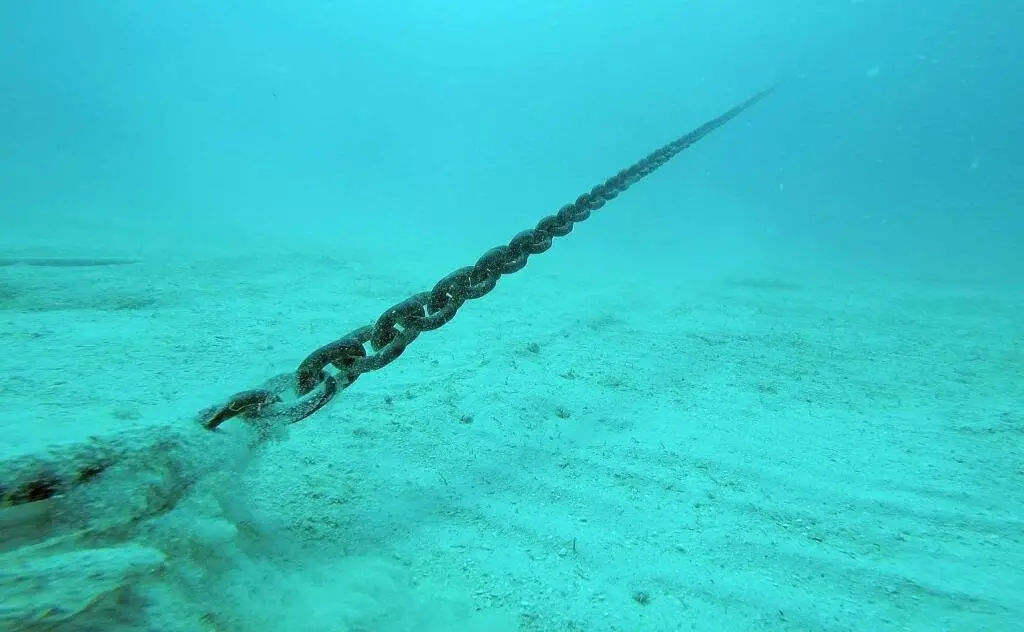
Anchor Holding to Seabed
Pic Courtesy: Sailmagazine
Mooring components of a CALM system:
- Anchors (piles- or gravity anchors connects the mooring chain to the seabed)
- Anchor chain (systems with six or eight anchor chains are the most common)
- Chain stoppers (connects the chains to the buoy)
Product Transfer System
The heart of each SPM is the product transfer system. This system transfers products from the tanker to the PLEM (Pipeline End Manifold) located on the seabed.
The basic product transfer system components are:
- Flexible subsea hoses also referred to as Risers which connects the PLEM to the Buoy. The configuration varies on depth, sea state, buoy motions, etc. and can take the form of a Chinese lantern, lazy-s, lazy wave or steep-s
- Floating hose strings which connect the buoy to the tanker.
- Marine breakaway coupling which allows for emergency disconnection of the pipeline to prevent rupture of hoses/hawser and subsequent oil spills.
- Product swivel, valves and piping connecting the geostatic and rotating parts of the buoy and enables the tanker to rotate with respect to the mooring buoy.
Other Components of SPMs
- A boat landing, providing access to the buoy deck.
- Fenders to protect the buoy.
- Lifting and handling equipment to aid materials handling.
- Navigational aids for maritime visibility, and fog horn to keep moving vessel alert.
- Electrical subsystem power navigation aids or other equipment. Electrical power can be provided either by batteries which are recharged on a regular basis or solar power systems to maintain the charge in the battery packs.
- Options are available for a hydraulic system to allow the remote operation of the PLEM valves if required.
Preparation for Mooring Operation (Ship to SPM buoy)
Adequate personnel under the supervision of a certified officer must be available for the following:
- Handling of equipment and gear.
- Communications.
- Directing the winch driver.
The deck crew shall be properly briefed prior to conducting the operations. Proper means of two-way communication shall be established between the stations and the bridge. Alternative means of communication shall also be kept ready if available. A visual contact and proper communication shall be established between the officer in charge and winch operator at the mooring station. Winch operator shall not be involved in any other operations except when he has been told so by Officer in charge.
Mooring winches, windlass and other associated machinery shall be tried out and kept ready before the actual operation commences. Hydraulic systems should be started well in advance in cold climates, for the oil to be at the optimum operating temperature.
At least one of the emergency towing arrangements shall be pre-rigged ready for rapid deployment. The condition of mooring equipment and lines shall be checked before use. Defective lines shall not be used. Adequate lighting should be available and key personnel should carry flashlights of the approved type. A new or inexperienced seaman or cadet shall not be used for handling ropes and wires during any critical operation until they have been trained.
Personal Protection Gear
All persons involved in mooring operations shall be adequately clothed and shall put on safety helmets with chinstraps, gloves, safety boots/shoes and other relevant safety gear. Well-fitting gloves and overalls should be used, to prevent these getting fouled in moving machinery.
Precaution during Mooring
Some associated tasks involving a high risk of personal injury are:
- Handling of ropes under tension when casting off, heaving in or slacking.
- Transfer of ropes from drums or bitts and vice versa.
- Use of stoppers
Precaution at Mooring Stations
- Stay clear of lines under load or tension when not handling them.
- Stay clear of mooring winches, drums and bitts with lines under tension on them. When handling the line on the warping drum, capstan or bitt, the handler must not stand close to the drum.
- Never stand on ropes or in their bights.
- Stay clear of the snapback or whiplash zones (area covered by the broken end of the line under recoil). If activity in this zone cannot be avoided, the exposure time should be minimal.
- Do not keep loose objects near the area where lines are being handled.
- If the line takes charge (uncontrolled running out of line under tension), do not attempt to stop it physically.
- When making fast towlines the personnel onboard should be able to communicate with the tugs verbally or using hand signals to convey the status of the line to the Tug Master. Stay clear of towlines made fast onboard.
- All personnel at mooring stations shall be alert and maintain an all-around vigil for any danger of ropes/wires parting after they are made fast onboard.
- Protect ropes from chafing on sharp edges.
- Avoid leading ropes at sharp angles or turns, to prevent loss of strength.
- It is the responsibility of the officer on station to keep the bridge updated about clearances between the vessels and other objects.
- Beware of the danger of ropes fouling propellers/bow thrusters if too much slack is lowered into the water.
- It is the responsibility of the officer on aft stations to keep the bridge informed whenever the propeller is not clear for engine movements.
- The operating area at the winches and the walkways on deck should be painted with anti-skid paint, the edges of these areas shall be highlighted with a contrast colour.
Mooring Arrangement Background
The hawser arrangement on the SBM usually consists of nylon rope, which is shackled to an integrated mooring uni-joint on the buoy deck. At the tanker end of the hawser, a chafe chain is connected to prevent damage from the tanker fairlead. A load pin can be applied to the mooring uni-joint on the buoy deck to measure hawser loads.
Hawser systems use either one or two ropes depending on the largest size of vessel which would be moored to the buoy. The ropes would either be single-leg or grommet leg type ropes. These are usually connected to an OCIMF chafe chain on the tanker side (either type A or B depending on the maximum size of the tanker and the mooring loads). This chafe chain would then be held in the chain stopper on board the tanker.
A basic hawser system would consist of the following (working from the buoy outwards):
- Buoy-side shackle and bridle assembly for connection to the pad-eye on the buoy;
- Mooring hawser shackle;
- Mooring hawser;
- Chafe chain assembly; Support buoy;
- Pick-up/messenger lines; Marker buoy for retrieval from the water.
Preparations from the vessel
- A messenger line is requested for pick up rope. It must be installed in an empty drum at the bow, enough to store a 120m [ or longer as per terminal advise] Pick Up Rope.
- Messenger must be 100 m length [or as advised by the terminal] and 1”-3” width with a small shackle at the end.
- Afterdeck: 02 X 200 Mt. to be used to Tug Boat
Procedure for mooring
The vessel under the advice of the Pilot or the Mooring Master will head slowly towards the buoy usually stemming the tide/currents./winds, which is normally the direction in which the hose string is leading and tug may be used at some terminals to ‘ nudge the bow ‘ into position.
At about 120 meters from the buoy the messenger [ which is reeved via the smits’ bracket [ or similar] ] is connected to the hawser and slowly heaved up, the duty officer/ Chief Officer and the mooring Master’s assistant will at all times be giving the distance and direction from the buoy.
When the optimum approach route has been selected, the vessel should proceed toward the SBM at a suitable speed dependent upon the conditions at that time. Approximately 1000 meters from the SBM, the vessel should have only sufficient speed for steerage.
The floating hose string should be held away from the tanker by support boat on the side at which the hose will be connected to manifold. The vessel should make the final approach with the buoy on the bow, rather than dead ahead. This permits the Pilot and the Master on the bridge to observe the buoy at all times, and in the event of any misjudgement of the approach speed, there is no danger of overrunning the buoy The tug if available may be used as required. The tanker’s approach speed must be reduced to a minimum, but sufficient to keep the ship’s manoeuvrability.
Hawser Connection
As the vessel approaches the berth, the floating hose is towed away from the path of the approaching tanker. When the vessel is approximately 300+ meters from the buoy, and still making way, the support boat will bring the hawser pick up rope (80 mm diameter) and make it fast to the messenger. At the boat’s signal, the pickup rope is heaved on deck.
The vessel should be brought to a dead stop between 45 and 60 meters (150 and 200 feet) from the buoy. At this point, the chafing chain is lifted into the bow chock and then to the bow chain stopper to be secured under the direction of the pilot. The Mooring Master or assistant and ch. Officer who are forecastle of the vessel and reports the distance and the position of the SPM in relation to the vessel to the Bridge during mooring operations.
The messenger /pick up rope is directly spooled onto the empty winch drum as also the hawser which is leading from the buoy. When the chafe chain comes to the Smit’s bracket the locking bar is placed and a safety pin is put through. At this time the ship is considered moored.
CAUTION
Under no circumstances must any load be put on the pick‐up rope as this will adversely affect the maneuverability of the vessel and eventually lead to the failure of the rope. The use of the pick‐up rope to heave the vessel or maintain the vessel’s position is not recommended.
Ease back on the pick‐up rope until the weight is taken up.
Monitoring the SBM position
After the ship is moored it is very important to note the location of the SBM vis a vis the ship and a lookout must be permanently stationed observing the location of the SBM and report to the CCR as per the following diagram.
Cargo Connections
The submarine hose will be connected and disconnected to the ship’s manifold with the ship’s crane as per directions from the Mooring Master.
Unmooring Procedure
After the Master has confirmed to the Pilot that the engines and the vessel are in all respects ready for unmooring, the unmooring will commence. The winches are to be checked prior to disconnection of the moorings. The pins to the bow stopper are removed and upon instruction, the weight is taken up on the mooring winch. The bow stopper is disconnected and secured, in the open position, before walking back the moorings. Slowly walk back the pickup rope until the support buoy is in the water and taking all the weight off the chain. Pay out the pickup line and do not disconnect the messenger until the pick‐up rope is completely slack and sufficient length is in the water. Ship staff to disconnect the messenger rope and at times it may be necessary to release the two moorings either together or individually.
Additional Precautions
- Monitoring of the weather and tides/currents especially when there is no tug available and constant monitoring of the SBM position will lead to a safe stay at the berth.
- The duty officer must NOT hesitate to stop cargo operations if there is an excessive strain on the hawser rope as once the hawser parts the entire weight will transfer onto the hose strings which will not last for long and the hose may part leading to an oil spill etc.
- The main engine to be on absolute readiness at all times.
- Pull back Tug: Many Terminals use a pull back tug which is made fast to aft centre lead of the ship, to keep a constant pull with due consideration to the prevailing winds and tides/currents, in order to avoid vessel from riding on to the buoy especially in confused conditions of the weather/seas.
good praticle , we learn more about SPM
work on SPM in west africa now。
Dear Sirs
we have a situation where the disconnection procedure of an oil tanker from the spm is not available as the company which installed the spm has closed down
the oil pipeline from shore to spm are disconnected and now we need to disconnect the oil tanker from the spm, can some help us in providing a solution at a reasonable cost
regards
I have a design on your SBM, that will help alot, and sell your product way more to others in need of your SPM. Less polution on the Grease of chains.
Dimension of SPM – Buoy PLEM
Can the oil processing facilities be installed on MOPU and Tanker hooked on SBM for loading? Once it is filled, another Tanker come to ensure continuous production, as offshore stand lone production facilities without connecting to onshore anyone have such experience: emadawad1@outlook.com
Any one has conducting Training for Operation and Maintenance courses with practical included.